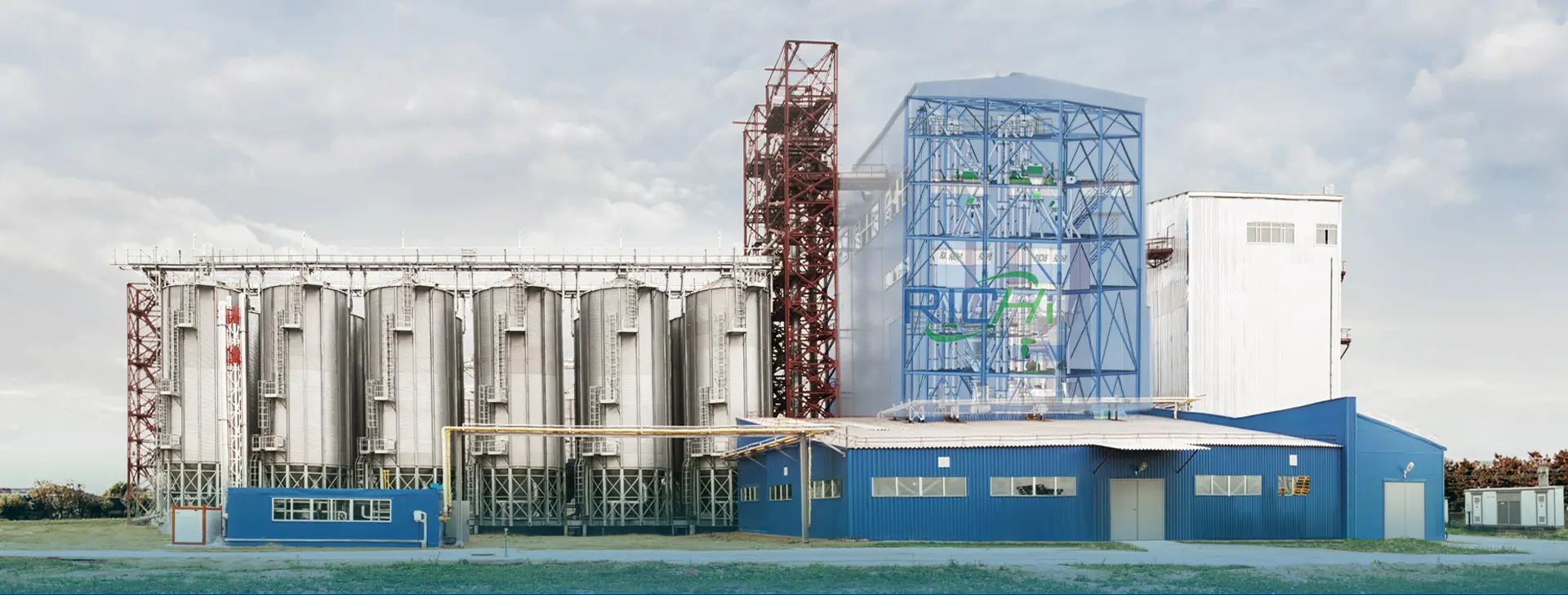
Complete Animal Feed/Pellet Production Line With Scalable Solutions
Realize your feed production with scalable solutions to improve the efficiency and quality of feed production with advanced RICHI Machinery.
Realize your feed production with scalable solutions to improve the efficiency and quality of feed production with advanced RICHI Machinery.
Start customizing your animal feed production line today. Just tell us your production needs, formula list, etc., and we can provide you with a complete feed production solution including silos.
Get QuoteWhether it's your company's plans or the market's needs, we can design a feed production line with different outputs depending on your needs. Just tell us what you need in terms of production capacity and RICHI Machinery will provide you with a turnkey solution.
Animal Feed Pellet Line Start From 1TPH
Animal Feed Pellet Line Start From 10TPH
Animal Feed Pellet Line Start From 30TPH
Essential for preparing and conditioning materials to ensure uniform quality before pelletizing.
learn more →The core process where prepared materials are compressed into dense, high-quality feed pellets.
learn more →Involves cooling, screening, and packaging to maintain pellet integrity and ready them for use or sale.
learn more →Supports the production line by enhancing material flow, reducing downtime, and maintaining operational efficiency.
learn more →We provide end-to-end support, from equipment supply to installation and training.
Our innovative machines ensure high efficiency, precision, and durability in production.
We tailor our solutions to meet your specific feed production needs and scale.
Proven track record with successful projects worldwide.
Dedicated after-sales service, ensuring smooth operation and continuous technical assistance
What kind of animal feed plant do you want to establish?
How many tons per hour about this plant you want to build?
Where is this animal feed plant going to be built?
When do you plan to start the operation?
Our feed production line is highly versatile, capable of producing a wide range of animal feeds to meet diverse nutritional needs. Here are the main types of feeds it can produce:
This flexibility ensures our feed production line can support various industries, providing high-quality feed for animals at every stage of life.
The animal feed production line is highly customizable to meet the specific needs of different customers and production requirements. Key customization options include:
These customization capabilities ensure that each production line is tailored to deliver optimal performance, cost-efficiency, and product quality.
The typical lifespan of our animal feed production equipment ranges from 10 to 15 years, depending on factors such as usage intensity, maintenance practices, and operating conditions. Regular maintenance and adherence to operational guidelines can significantly extend the equipment's longevity, ensuring consistent performance and reliability over time.
Yes, RICHI Machinery offers comprehensive installation and training services to ensure the optimal performance of your equipment. Our services include:
These services are part of our commitment to providing professional and convenient turnkey engineering solutions, from scheme design and equipment production to installation, training, and ongoing technical support.
Yes, our feed production lines are designed to handle a wide variety of raw materials, including grains, soybean meal, corn, wheat, oilseed meals, and even fibrous materials like straw and grass. The system's versatility allows it to process raw materials with different moisture content and particle sizes, ensuring efficient production of high-quality feed for various applications, such as poultry, livestock, and aquaculture. Additionally, the line can be customized to incorporate special ingredients, such as vitamins, minerals, and additives, to meet specific nutritional requirements.
The energy consumption of an animal feed pellet production line varies depending on several factors, including the scale of production, the type and moisture content of raw materials, and the specific equipment used. Here are typical energy consumption estimates for key components:
Depending on the setup, the total energy consumption typically ranges from 40 to 200 kWh per ton of finished feed. Investing in energy-efficient equipment and optimizing operational processes can significantly reduce energy costs while maintaining high production output.
Ensuring consistent pellet quality in the production line involves a combination of advanced technology, precise control, and best practices:
By integrating these strategies, consistent pellet quality is achieved, enhancing feed efficiency, product reliability, and customer satisfaction.
Proper maintenance is essential to ensure the efficiency, reliability, and longevity of a feed production line. Here are the key maintenance requirements:
Yes, spare parts are readily available for our equipment. We maintain a comprehensive inventory of high-quality replacement parts to ensure minimal downtime and seamless operation for our clients. Whether it’s blades, hammers, screens, or other wear-and-tear components, our global supply network ensures quick delivery and easy access. Additionally, our dedicated customer support team is always available to assist with selecting the right parts and providing maintenance guidance.
Controlling dust and waste in the animal feed production line is essential for maintaining a clean, safe, and efficient production environment. Here’s how it is typically managed.
By integrating these measures, animal feed production lines can effectively control dust and waste, ensuring a safe, efficient, and environmentally friendly operation.
If you need further information, please contact us
For all inquiries fill in the form below to send us a brief message,and we will get back to you as soon as possible
RICHI stick to the service principle is: We are focusing on your future, your future is our future!
© HENAN RICHI MACHINERY CO., LTD 1995-2025
Product Line-Up / Privacy Policy