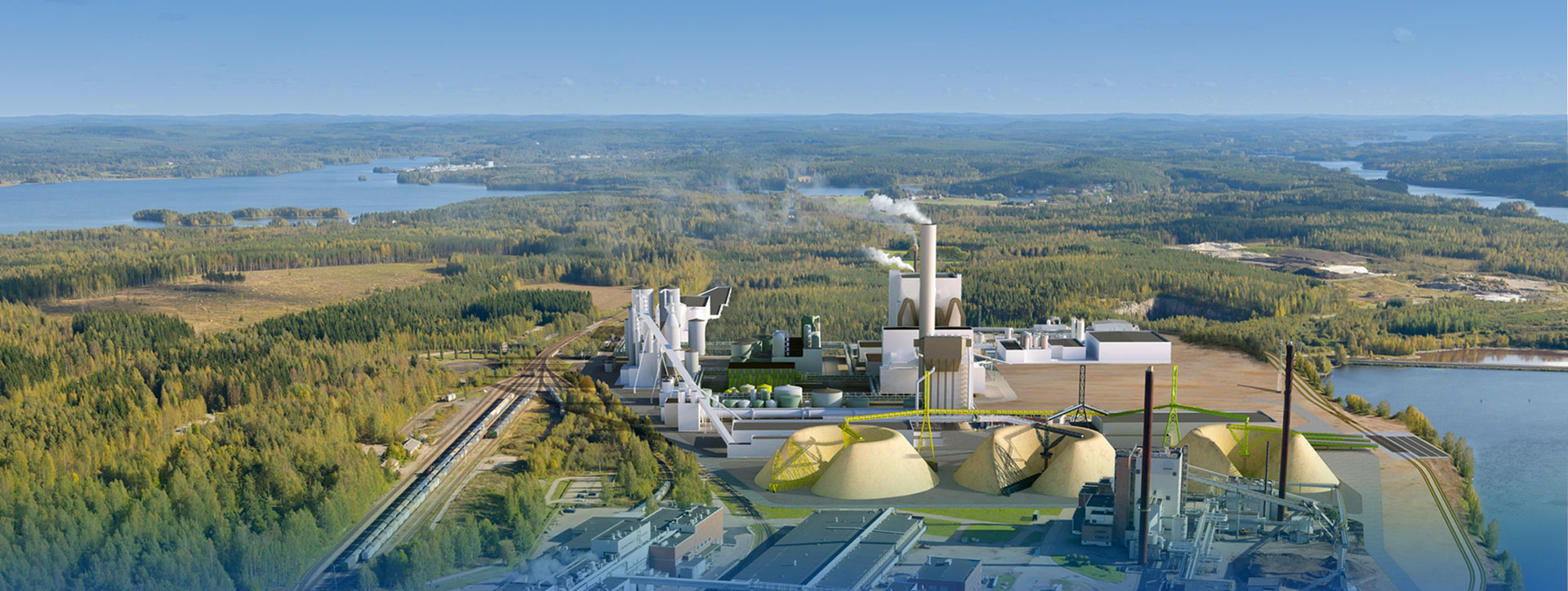
Complete Biomass Pellet Production Line With Scalable Solutions
Realize your feed production with scalable solutions to improve the efficiency and quality of biomass pellet production with advanced RICHI Machinery.
Realize your feed production with scalable solutions to improve the efficiency and quality of biomass pellet production with advanced RICHI Machinery.
Start customizing your biomass pellet production line now. Just tell us about your production needs, raw materials and more, and we can provide you with a complete biomass pellet production solution including raw material handling and more.
Get QuoteWhether it's your company's plans or the market's needs, we can design a biomass pellet production line with different outputs depending on your needs. Just tell us what you need in terms of production capacity, raw materials and RICHI Machinery will provide you with a turnkey solution.
Pelleting Solution For Biomass Materials Start From 1 TPH
Pelleting Solution For Biomass Materials Start From 3 TPH
Pelleting Solution For Biomass Materials Start From 6 TPH
Essential for preparing and conditioning materials to ensure uniform quality before pelletizing.
learn more →The core process where prepared materials are compressed into dense, high-quality feed pellets.
learn more →Involves cooling, screening, and packaging to maintain pellet integrity and ready them for use or sale.
learn more →Supports the production line by enhancing material flow, reducing downtime, and maintaining operational efficiency.
learn more →We provide end-to-end support, from equipment supply to installation and training.
Our innovative machines ensure high efficiency, precision, and durability in production.
We tailor our solutions to meet your specific feed production needs and scale.
Proven track record with successful projects worldwide.
Dedicated after-sales service, ensuring smooth operation and continuous technical assistance
What raw materials are you going to utilize for pelletizing?
How many tons per hour about this pellet plant you want to build?
Where is this biomass pellet plant going to be built?
When do you plan to start the operation?
A biomass pellet production line can process a wide variety of raw materials, primarily composed of organic and renewable resources. Below are the common types of raw materials used:
The versatility of raw materials makes biomass pellet production lines highly adaptable to different regions and industries, turning waste into valuable energy or raw material for various applications.
Moisture content plays a vital role in the pellet production process as it directly affects the binding of raw materials. During pelletizing, moisture helps soften the material, allowing it to compress and bond under high pressure within the pellet mill. The optimal moisture content, typically between 10-15%, ensures that the raw material forms durable and well-shaped pellets. If the moisture content is too low, the material will be too dry to bind effectively, resulting in brittle pellets that are prone to breaking.
Conversely, excessive moisture content can lead to several problems. High moisture causes the raw material to clump, increasing the risk of blockages in the pellet mill's die. This not only disrupts production but also puts additional strain on the machinery, accelerating wear and tear. Moreover, overly wet pellets tend to be soft and crumbly, compromising their durability and quality. To avoid these issues, pre-drying systems or moisture control technologies are often used to ensure raw materials are within the optimal moisture range before pelletizing.
In addition to affecting pellet formation and machine efficiency, moisture content significantly impacts storage and transport. Pellets with high moisture content are susceptible to mold growth and degradation, reducing their shelf life and usability. On the other hand, pellets that are too dry can produce excessive dust, which poses safety risks and reduces product quality. Maintaining the right moisture balance not only ensures efficient production but also results in high-quality pellets that are durable, safe, and long-lasting.
Yes, a biomass pellet line can handle multiple raw materials, but certain considerations are necessary to ensure efficient operation and high-quality pellet production.
The energy consumption of a biomass pellet production line varies widely depending on the type of raw materials, program design, equipment configuration, and production capacity. For instance, materials with high moisture content, such as agricultural residues, may require additional energy for drying, while denser materials like wood chips demand more power during grinding and pelletizing. Smaller-scale lines with lower output typically consume less energy, while large-scale, high-yield lines require more power to maintain efficiency. On average, energy consumption ranges from 50 kWh to 150 kWh per ton of pellets produced, depending on these factors. Our team customizes each production line to optimize energy use, ensuring cost-effective and sustainable operations for your specific needs.
Pellet size plays a crucial role in determining the effectiveness and suitability of biomass pellets for various applications. Here’s how different pellet sizes influence their use:
Yes, the biomass pellet production process is considered environmentally friendly mainly because of these factors: Utilization of renewable resources; Reduction of greenhouse gas emissions; Efficient waste management; Reduction of the environmental impact of production. Thus, the biomass pellet production process offers an environmentally friendly alternative to energy production, contributing to reduced dependence on fossil fuels, lower greenhouse gas emissions and sustainable waste management.
Using a ring die in pellet mills offers several advantages over a flat die, particularly for large-scale and industrial applications. Ring dies are designed for higher production capacities, enabling continuous operation with greater efficiency. Their structure allows for uniform distribution of material, resulting in more consistent pellet quality and density. Additionally, ring dies experience less wear and tear due to their circular motion, which reduces stress on individual parts, leading to a longer lifespan and lower maintenance costs. They are also more energy-efficient for processing harder materials, making them ideal for producing large volumes of high-quality pellets in industries such as animal feed, biomass, and aquaculture.
The frequency of maintenance for biomass pellet equipment depends on the intensity of use, the type of raw materials processed, and the specific components involved. Generally, routine maintenance, such as cleaning and lubrication, should be performed daily or weekly to prevent dust buildup and reduce wear on moving parts like rollers and dies. Monthly checks are recommended for inspecting wear-prone components, such as bearings, belts, and screens, to ensure optimal performance and avoid unexpected downtime. Additionally, major servicing should be scheduled every 6 to 12 months, focusing on more in-depth inspections and replacements of critical parts, such as the die and rotor, to maintain efficiency and extend the equipment’s lifespan. Proper adherence to these maintenance intervals ensures reliable operation and minimizes costly repairs.
Yes, integrating existing equipment into a new biomass pellet production line is often possible and can be a cost-effective solution. However, several factors must be considered to ensure seamless integration and optimal performance:
Integrating existing equipment into a new biomass pellet production line is feasible and can reduce initial investment costs. However, careful evaluation of compatibility, performance, and potential modifications is crucial to ensure a smooth and efficient production process.
If you need further information, please contact us
For all inquiries fill in the form below to send us a brief message,and we will get back to you as soon as possible
RICHI stick to the service principle is: We are focusing on your future, your future is our future!
© HENAN RICHI MACHINERY CO., LTD 1995-2025
Product Line-Up / Privacy Policy